 |
 | Mazda RX7 Conversion |  | Ian Hooper, 2012 | |
Drivetrain
Gearbox Adapter Plate
Where I left off in the Getting Started section, I had finished prototyping the motor cradle, and had ordered the laser cutting to make the final design from steel. Pictured right is almost a thousand dollars worth of laser cutting - though I suspect most of the cost was the 100 or so battery interconnectors! The motor cradle parts are the dark grey steel pieces (top middle), also pictured are the battery box panels.
Laser cutting is a great way to get complex, accurate parts done - generally much easier than making things by hand - and cheaper, if you count your time. For people in Perth, I usually use Total Laser Cutting Services. |
|
Firstly for the gearbox adapter plate, which fits between my motor cradle and the gearbox end section (which I am using for its speedometer sensor, and accurate tailshaft / torque tube alignment), I only had the basic shape laser cut. I then got High Speed Engineering to digitize the bolt pattern of the gearbox piece with respect to its tailshaft output, and used a milling machine with digital readout for precisely drilling the holes. The gearbox end section has a couple of 12mm dowel pins for accurate positioning, and half a dozen 12mm holes for M12 bolts, which fasten into threaded holes in the 12mm thick adapter plate.
Motor Cradle Assembly
I decided the best way to construct the motor cradle accurately would be to tack weld it together around the motors, then do final welding without the motors (so they don't get too hot, or get in the way). The pics below show test assembly of the pieces, clamping them to one of the motors, and tack welding them in-situ.
Once the frame was tack welded together, I did a test-fit of both motors including Rotex coupling, to verify both fit and alignment. I then tack welded together the two "legs" which support the cradle upon the original engine mounts, and the central brace which improves rigidity between the motors. The third photo shows the assembly including the gearbox end section. (At this point the legs are just sitting in place, not actually attached.)
Next I completed the final welding of the central frame section (a couple of pics showing the welding below). For welding I use a 200A TIG, which is probably slower than MIG (or stick) but tends to offer the neatest welds - and arguably strongest. I also did the final welds of the support legs - still separate from the rest of the cradle - then installed the pieces in the car and measured/marked the locations.
The following three pictures just show tack welding then final welding of the support legs on to the rest of the frame, then another test fitting of the motor cradle in the engine bay. It fit perfectly - phew! (NB: You can't seem the in the photo, but there are large rubber vibration absorbers between the cradle legs and the chassis mounts.)
One caveat worth mentioning .. As it turned out, presumably due to a tiny amount of distortion from welding, the motors were just too tight a fit to get back into the cradle after final welding! Not good. I ended up having to shorten the motors by about half a millimetre. Doesn't sound like much, but with such a rigid frame it made all the difference between fitting and not fitting. Shortening the motors slightly actually wasn't as hard as it sounds. I just had to remove the commutator-end casting from the motors and trim the inner side of this in a lathe. Anyway, if I built another I'd be sure to put in half a mm of shim when doing the initial tack welds, for a small amount of tolerance/clearance.
Motor/Tailshaft Coupler
Basically, I need to couple the motor output shaft to the tailshaft somehow for it to move the car. In my old MX5 I had a custom tailshaft made which fastened to the motor directly, but for the RX7 I decided it would be easier/better to use the end section of the original gearbox, as well as the original gearbox output shaft with spline. For this I just need to use the original gearbox output shaft, and make a couple to attach it to the motor. It's a pretty simple design, pictured right.
Rotomotion were kind enough to give me a broken old RX7 gearbox which I could use use the pieces from, rather than butcher my working gearbox (which has resale value). Trying to cut the old gearbox output shaft off was interesting; the steel was so hard that my bandsaw couldn't scratch it - the blade just slid over the surface! It had to be cut off with a friction cutter (i.e angle grinder with cutting disc). |
|

The original output shaft of gearbox, and steel piece for coupler
Since I have neither a broaching machine for cutting internal keyways, nor a great deal of confidence in my ability on a lathe to make something like this accurately, I was going to outsource its fabrication. But after speaking with Kim at Wattle Grove Engineering, who explained how I could do internal keyways on my lathe, and suggested a method of making the coupler in two parts and welding together, I thought I might give it a go. Good practice/experience if nothing else.
Firstly, inside keyways can be done on a normal lathe by locking the chuck in place, using a boring bar with tool steel the size of the keyway, running the boring bar back and forth manually using the carriage, taking tiny incremental cuts by moving the cross slide slightly after each pass. As for the fabrication, he suggested making the coupler in two halves, which makes it easier to cut the keyways (since the larger one wouldn't be butting up against a shoulder its inner end), and cutting a big chamfer where the two meet for a nice deep weld groove. Then machine an insert which fits inside both halves exactly to hold them in precise alignment during welding (and while cooling after).
However the next steps did not go so well. My mill's cutting tools had a great deal of trouble cutting a keyway into the gearbox output shaft (other than the first few MM, which had probably lost its temper when the friction cutter did its work). And the system of cutting an inside keyway on a lathe using a boring bar and the carriage was painfully slow. So in the end I got Luke at EV Works to do the coupler for me. Oh well, at least I tried.
Oil Circulation for Tailshaft Bushing
The gearbox end section has a bushing which the tailshaft slides into. This is intended to be lubricated with gearbox oil, and includes a channel to carry oil to it. But since I'm only using the end section, there wasn't necessarily any oil in there - and the bushing would probably overheat without it (making it squeal and wear out at best, or seize up at worst).
I considered modifying the end section to use a ball bearing instead, but it would actually be a fair bit of work chopping the bushing off, fabricating a bearing mount, and ensuring the alignment remained perfect. So I decided the best option was to add some oil, and a means of throwing the oil into the channel which runs down to the bushing. (Some people had suggested that with enough oil in there it would slosh back to the bushing whenever I accelerated, but I was still concerned about the bushing drying out with extended highway use at steady speed.)
After a bit of pondering, I decided on a couple of gears, one mounted to the driveshaft coupler and another below, with its teeth picking up oil off the lowest part of the gearbox section. Below you can see my initial sketch based on measurements of the gearbox section, then a 1:1 wood mockup I made to verify the fit. A couple of plastic gears were procured from RS components - the third picture shows these, and some 12x6 bearings for mounting the lower gear.
Below you can see the modified gears, one with bearings added and the other a press fit engaging onto a small shoulder I machined into the driveshaft coupling. The gears aren't really taking any torque so I figure an interference should suffice. I then carefully drilled and tapped a threaded (M6) hole into the adapter plate, and fastened the idler gear on. In the third picture you can see the alignment of the gears verified.
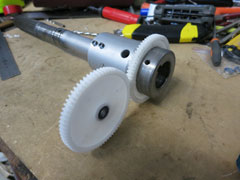
Modified gears: Bearings and fit to coupler |
|
|
Installing The Motor Assembly
The way the motor frame was originally designed left me no choice but to install both motors simultaneously. After spending an infuriating hour or two trying to get the motors in, I came to the conclusion that maintaining simultaneous perfect alignment of two heavy motors in such a tight-fitting frame was not going to happen. So I modified the frame to allow the motors to go in one at a time.
A few minutes with the angle grinder had the front end plate of the motor frame removed as per the first picture below. I then made up a couple of mounting tabs which were welded to the end plate, and screwed in to the rest of the frame. With this end plate removable, I could install the rear motor first then front motor, separately. The other final modification I made to the frame was to add a skid plate / bash guard, to protect the adaptor plate (since it extended below the main motor frame rails by a few centimetres, and I was concerned it could catch on something and be damaged).
The three pictures below show the installation of the rear motor first (inverted and attaching frame onto motor, since the latter is much heavier and harder to maneuver), then installing the second motor, then after installing the central brace and righting the assembly with an engine crane, tapping on the driveshaft coupler.
Before the gearbox section could be installed, I put the speedometer drive gear back on (first picture below). Then I fastened the gearbox section to the adapter plate (second picture), and then bolted these up the the motors (third picture). To my great relief, the alignment appeared to be perfect, without any tight spots as I turned the central Rotex coupler by hand. Phew!
A quick note on shaft alignments: Effectively the motor assembly has four bearings and a bushing all in one line. A good "rule of thumb" is to never have more than two bearings on the same rigid shaft, in case either the shaft or the bearings are not in perfect alignment. This was the reason for the Rotex coupling between the motors, which features two metal jaws and a polyurethane "spider" between them, allowing about a millimetre of radial and a couple of degrees of angular misalignment. So they still must be pretty close to aligned, but a little flex won't cause any problems.
A more critical alignment was the bushing for the tailshaft yoke being perfectly aligned with the two motor bearings - which is kind of three rigid bearings in a line! The adapter plate design was based on digitised measurements off the gearbox section, drilled with a digital milling machine (both very accurate), and had a couple of dowel pins into the gearbox piece for accurate alignment, but bolting the adapter plate to the motor assembly could introduce a bit (fraction of a mm) of misalignment due to play in the bolt holes, which might have been enough to cause problems with such a rigid tailshaft coupler. To combat this I had a slip yoke on the output spline / in the bushing while I bolted things up to hold the alignment correct. The main remaining concern was that the motor coupling could have been slightly out of true, which would've caused a cyclic tight spot - or simply that a mistake had been made somewhere in the digitising, CAD design or machining of the adapter plate. But thankfully it all seemed good. |
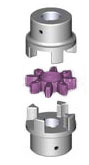 |
Since the rear motor would be a fair way down in the gearbox tunnel, I figured I should do the motor power wiring before installation. I'll describe the wiring in more detail in the Electrical section later, but for now here's a picture of the reversing contactor mounted, and all the motor wiring completed. The attachments to the Zilla come off one terminal of the reversing contactor, and the front-most motor terminal, which are both readily accessible later.
With the motor assembly complete, I enlisted the help of my brother with the careful job of installing the assembly in the engine bay. He manned the engine crane while I maneouvered the assembly in. Below you can see a few pictures from the procedure.
|
|
Continue reading --> Battery Packs
Comments | Coulomb on 26th Jun 2012 Minor web page nit: "Laser Cut Gearbox Adapter Plate" links to the wrong image. The laser cutting is really neat. | |  | | Ian Hooper on 27th Jun 2012 Link fixed! Thanks. |
|
| eBEEMER on 30th Jun 2012 Hi Ian
If it's not too late, it's a good idea to leave a couple of mill clearance between the shaft ends as an expansion allowance.
Looks like a great job. |
| Weber on 16th Jul 2012 Well done, Ian!
For lubricating the tailshaft bush, won't it be sufficient that you first fill the gearbox tail-casing with oil until it just runs out the bush when on a horizontal surface with the tailshaft out. Then whenever you accellerate or go uphill it will slosh back there.
I remind you of this AEVA thread which also considered the opposite problem of keeping the oil out of the motor, and suggested some off-the-shelf precision rigid couplings.
http://forums.aeva.asn.au/forums/forum_posts.asp?TID=961&PID=9316#9316 |
| Weber on 13th Aug 2012 Great work as usual Ian. It would be good to see a close-up of the Rotex flexible coupling, or to link to an exploded view like the one here http://www.ktr.com/en/products/couplings/rotex/standard.htm
This might help to make new DIY converters aware of the "No more than 2 bearings per rigid shaft" rule. You wrote "To my great relief, the alignment appeared to be perfect, without any tight spots as I turned the central Rotex coupler by hand." But of course the reason you used a flexible coupler is so it didn't _need_ to be perfect, since it never will be, or will never stay that way. But it still needs to be within fairly tight tolerances, and _that_ is what you were relieved to find. | |  | | Ian Hooper on 13th Aug 2012 Thanks for the comments. Good idea about the "2 bearings per rigid shaft" bit - I'll insert some more info about shaft/bearing alignments somewhere.. The Rotex coupling means alignment between the motors didn't have to start or stay perfect, but the tailshaft bushing and two rear motor bearings are effectively all on one rigid shaft! So for that I was counting on the adapter plate and motor coupling all being spot on (or at least close enough not to cause problems). |
|
| Weber on 14th Aug 2012 Although your SOGOS (sawn off gearbox output shaft) is rigidly coupled to your motor shaft, it still obeys the "max 2 bearings per rigid shaft" rule because there is a flexible coupling that you're not recognising, in between the SOGOS and the tailshaft bushing, namely the spline coupling. If you had slid the tailshaft onto the SOGOS before you put the gearbox end section in place, you should have found a small amount of angular free-play between the two shafts which, in a spline, implies also radial free-play. And of course its axial free-play is obvious. But it allows for far less free play than your rotex coupling, maybe only 100 um, so the motor to adapter-plate and adapter-plate to gearbox-end-section should be located with something other than their bolts. As Newton (Jeff Owen) is fond of saying, "Bolts retain, they don't locate". I notice you have locating pins between the gearbox-end-section and the adapter-plate, but what do you have locating the adapter-plate to the motor? | |  | | Ian Hooper on 14th Aug 2012 I found that the yoke on the spline was fairly play-free (your 100um is probably about right, maybe even less) and the yoke in the bushing was very close tolerance (bearing-like, no detectable play). So with the yoke in the bushing and on the spline as I slid the gearbox section into place, there seemed to be minimal play between adaptor plate and motor assembly. The SOGOS is super hard steel and wouldn't bend much with the weight of the gearbox section on it, but I did try to support the weight of the gearbox section to remove any load on the SOGOS while bolting the adaptor plate to motor assembly. FWIW there wasn't an appreciable increase in torque required to turn motors over before and after the gearbox section was bolted on, which hopefully means things are straight and aligned. But I agree that a couple of locator dowel pins between motor assembly and adaptor plate would have been better. |
|
|